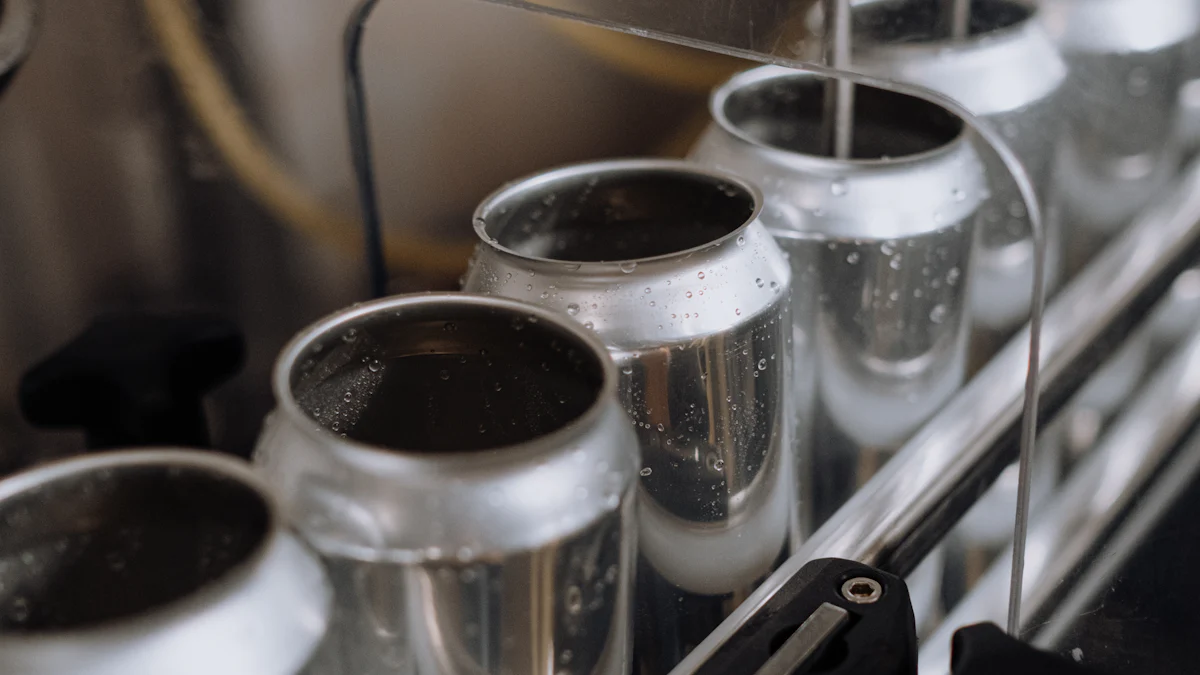
Twin Screw Extruders play a vital role in modern manufacturing, serving as essential tools in industries such as food, medical, pharmaceutical, and plastics. These machines enhance production processes by offering unparalleled efficiency and versatility. In 2023, the global twin screw extruder industry reached a valuation of US$ 1.25 billion, highlighting their significant impact. The Asia Pacific region leads the market, accounting for over 43% of total sales. This widespread adoption underscores the importance of twin screw extruders in improving product quality and streamlining operations across various sectors.
Food Industry
Applications in Food Processing
Snack Production
The Twin Screw Extruder plays a crucial role in snack production. Manufacturers use these machines to create a variety of snacks, including chips, crackers, and puffed products. The extruder’s ability to handle different ingredients and produce complex shapes makes it indispensable in this sector. By controlling the pressure and shear force, the Twin Screw Extruder ensures that snacks have the desired texture and flavor. This versatility allows producers to innovate and meet consumer demands for new and exciting snack options.
Cereal Manufacturing
In cereal manufacturing, the Twin Screw Extruder is essential for producing breakfast cereals. It processes grains and other ingredients into various shapes and textures, such as flakes, puffs, and rings. The extruder’s precision in mixing and cooking ensures consistent quality in every batch. This consistency is vital for maintaining brand reputation and customer satisfaction. Additionally, the Twin Screw Extruder allows manufacturers to incorporate additional nutrients and flavors, enhancing the nutritional value and taste of cereals.
Benefits in Food Industry
Consistent Product Quality
The Twin Screw Extruder offers significant advantages in maintaining consistent product quality. Its advanced mixing capabilities ensure uniform distribution of ingredients, resulting in a homogeneous product. This consistency is crucial for meeting industry standards and consumer expectations. By providing precise control over processing conditions, the Twin Screw Extruder minimizes variations in texture, flavor, and appearance, ensuring that each product meets the desired specifications.
Enhanced Production Efficiency
Efficiency is another key benefit of using a Twin Screw Extruder in the food industry. These machines streamline the production process by combining multiple operations, such as mixing, cooking, and shaping, into a single step. This integration reduces production time and energy consumption, leading to cost savings for manufacturers. The Twin Screw Extruder also allows for continuous processing, which increases output rates and reduces downtime. As a result, manufacturers can meet high demand while maintaining quality and efficiency.
Medical and Pharmaceutical Industry
Use in Drug Manufacturing
Continuous Processing
In the pharmaceutical industry, the Twin Screw Extruder revolutionizes drug manufacturing through continuous processing. This method allows for the uninterrupted production of medications, enhancing efficiency and reducing production time. By maintaining a steady flow of materials, the Twin Screw Extruder ensures consistent quality and uniformity in drug formulations. This continuous approach minimizes the risk of contamination and improves the overall safety of pharmaceutical products.
Improved Drug Formulation
The Twin Screw Extruder excels in improving drug formulation by offering precise control over mixing and processing conditions. It enables the integration of active pharmaceutical ingredients (APIs) with excipients, resulting in enhanced drug delivery systems. This capability allows for the creation of innovative dosage forms, such as controlled-release tablets and capsules. The extruder’s versatility in handling various ingredients ensures that pharmaceutical companies can develop customized formulations to meet specific therapeutic needs.
Benefits in Medical Applications
Precision and Consistency
Precision and consistency are paramount in medical applications, and the Twin Screw Extruder delivers on both fronts. Its advanced mixing capabilities ensure the even distribution of ingredients, leading to uniform products. This consistency is crucial for maintaining the efficacy and safety of medical devices and drug delivery systems. By providing precise control over processing parameters, the Twin Screw Extruder minimizes variations, ensuring that each batch meets stringent quality standards.
Cost-Effectiveness
The Twin Screw Extruder offers significant cost-effectiveness in medical manufacturing. By streamlining multiple processes into a single step, it reduces production costs and energy consumption. This efficiency translates into lower operational expenses for pharmaceutical companies. Additionally, the extruder’s ability to handle complex formulations with ease reduces material waste, further contributing to cost savings. As a result, manufacturers can produce high-quality medical products at a competitive price, benefiting both the industry and consumers.
Plastics Industry
The plastics industry heavily relies on the Twin Screw Extruder for its advanced capabilities in processing and manufacturing. These machines have revolutionized plastic production by offering superior mixing, flexibility, and control over process parameters compared to traditional methods.
Role in Plastic Compounding
Polymer Blending
In plastic compounding, the Twin Screw Extruder excels at polymer blending. It efficiently combines different polymers to create materials with desired properties. This blending process is crucial for producing plastics with specific characteristics, such as strength, flexibility, or heat resistance. The extruder’s ability to handle various polymers ensures that manufacturers can develop customized solutions for diverse applications, from automotive parts to consumer goods.
Additive Incorporation
The Twin Screw Extruder also plays a vital role in additive incorporation. It allows for the precise integration of additives, such as colorants, stabilizers, and fillers, into the polymer matrix. This capability enhances the material’s properties, improving its performance and durability. By controlling the distribution of additives, the extruder ensures uniformity and consistency in the final product, meeting the stringent quality standards of the plastics industry.
Advantages in Plastics Manufacturing
Enhanced Material Properties
One of the significant advantages of using a Twin Screw Extruder in plastics manufacturing is the enhancement of material properties. The extruder’s superior mixing capabilities ensure a homogeneous blend of polymers and additives, resulting in improved mechanical and thermal properties. This enhancement allows manufacturers to produce high-performance plastics that meet the demands of various industries, including automotive, aerospace, and electronics.
Energy Efficiency
Energy efficiency is another key benefit of the Twin Screw Extruder. These machines optimize the extrusion process by reducing energy consumption while maintaining high output rates. Their design allows for efficient heat transfer and precise control over processing conditions, minimizing waste and maximizing productivity. This energy efficiency not only lowers operational costs but also contributes to sustainable manufacturing practices, aligning with the industry’s growing focus on environmental responsibility.
Twin screw extruders stand as pivotal tools in modern manufacturing, driving efficiency and innovation across various industries. Their versatility allows them to handle diverse materials and formulations, making them indispensable assets for manufacturers. By offering improved mixing capabilities and precise control over process parameters, these machines ensure consistent and high-quality end products. The ability to streamline complex procedures enhances productivity and economic opportunities. As industries continue to evolve, the role of twin screw extruders in optimizing production processes and improving product quality remains crucial.
See Also
Exploring Various Categories of Extrusion Machines
Advancements in the Hollow Blow Molding Machine Sector
Maximizing Barrel Temperature Efficiency in Single-Screw Extruders
Emerging Trends in China’s Machinery: Sustainable Pelletizing Solutions
Jinteng Screw Barrel: Driving Forces Behind Industrial Innovation
Post time: Nov-15-2024