The role of the extruder screw in the extruder
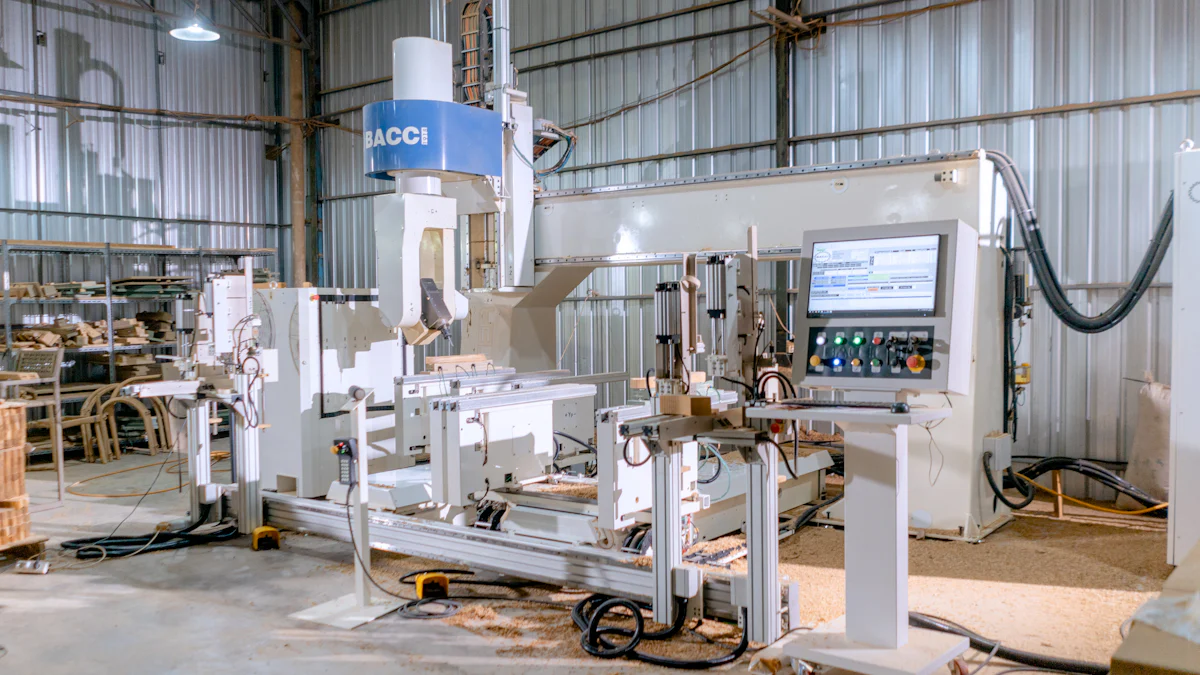
The extruder screw serves as the “heart” of the extruder, playing a pivotal role in the extrusion process. It performs three primary functions essential for effective material processing:
- Conveying Materials: The screw transports polymer resin through the extrusion barrel, ensuring a steady flow towards the die.
- Melting Materials: As the screw rotates, it generates heat, melting the resin and preparing it for shaping.
- Mixing Materials: The screw’s design enhances the blending of materials, crucial for achieving a homogeneous product.
These functions significantly influence product quality and processing efficiency, making the extruder screw indispensable in the extrusion industry.
Primary Functions of the Extruder Screw
The extruder screw plays a vital role in the extrusion process, performing several key functions that ensure efficient material processing. Understanding these functions helps in appreciating the significance of the extruder screw in manufacturing.
Conveying Materials
The primary task of the extruder screw involves transporting materials through the extrusion barrel. As the screw rotates, it pushes the polymer resin forward, ensuring a consistent flow towards the die. This movement is crucial for maintaining a steady production rate and achieving uniform product quality. The design of the screw, including its length-to-diameter ratio, directly impacts its ability to convey materials effectively. A well-designed screw ensures optimal throughput and minimizes the risk of blockages.
Melting Materials
Melting materials is another critical function of the extruder screw. As the screw rotates, it generates frictional heat, which melts the polymer resin. This process prepares the material for shaping and forming. The efficiency of melting depends on the screw’s geometric parameters, such as its compression ratio and profile. These factors influence the heat generation and distribution within the extrusion barrel. Proper melting is essential for producing high-quality products with consistent properties.
Mixing Materials
The extruder screw also plays a significant role in mixing materials. Effective mixing ensures a homogeneous blend of polymers and additives, which is vital for achieving the desired product characteristics. The screw’s design, including its groove feed and screw profile, enhances its mixing capabilities. Longer screw systems improve homogenizing performance, although they may increase the risk of material degradation. Therefore, selecting the appropriate screw design is crucial for optimizing mixing efficiency and maintaining product integrity.
Scientific Research Findings:
- Understanding the Intricacies of Extruder Screws in Plastic Extrusion highlights the importance of screw design in optimizing the extrusion process.
- The Role of Screw Design in Extrusion Machine Performance emphasizes the impact of geometric parameters on extrusion efficiency.
The extruder screw’s ability to convey, melt, and mix materials significantly influences the overall performance of the extrusion process. By selecting the right screw design, manufacturers can enhance product quality and maximize production efficiency.
Design Aspects of the Extruder Screw
Length-to-Diameter Ratio
The length-to-diameter (L/D) ratio of an extruder screw plays a crucial role in its performance. This ratio refers to the proportion between the screw’s length and its diameter. Historically, the first patents for rubber extruder screws, developed by inventors like Mathew Grey and Francis Shaw, featured short L/D ratios ranging from 3:1 to 6:1. These early designs focused on creating compression through deep channels and a decreasing lead angle.
Increasing the L/D ratio enhances the screw’s ability to process materials effectively. A longer screw provides more time for the material to melt and mix, improving plasticization quality. This extended length allows for better temperature distribution, which is essential for the mixing and plasticization of plastics. Manufacturers often adjust the L/D ratio to optimize the screw’s performance for specific materials and applications.
Material Selection
Material selection for extruder screws is another critical design aspect. The choice of material affects the screw’s durability, wear resistance, and overall efficiency. Manufacturers typically use high-strength steel alloys for their excellent mechanical properties and resistance to wear and corrosion. These materials ensure that the screw can withstand the high pressures and temperatures encountered during the extrusion process.
In some cases, manufacturers may apply surface treatments or coatings to enhance the screw’s performance further. These treatments can improve wear resistance and reduce friction, leading to increased efficiency and longer service life. Selecting the appropriate material and treatment for an extruder screw is vital for maintaining optimal performance and ensuring the longevity of the equipment.
Types of Extruder Screws
Single Screw Extruders
Single-screw extruders serve as the most common type in the extrusion industry. They consist of three main sections: the extrusion system, the transmission system, and the heating and cooling system. Each section performs a distinct function, contributing to the overall efficiency of the extrusion process. The screw’s length, diameter, pitch, and depth vary across these sections, affecting the extruder’s performance. Single-screw extruders efficiently convey, melt, and mix materials, making them suitable for a wide range of applications. Their simplicity and cost-effectiveness make them a popular choice for many manufacturers.
Twin Screw Extruders
Twin-screw extruders feature two parallel screws rotating inside the same barrel. This design offers increased flexibility and superior control compared to single-screw extruders. The screws can either rotate in the same direction (co-rotating) or in opposite directions (counter-rotating). Twin-screw extruders excel in mixing and plasticizing materials, making them ideal for complex processing tasks. They can compound materials fed into the barrel, enhancing the extrusion process’s efficiency. The intermeshing screws provide better mixing capabilities, ensuring a homogeneous blend of polymers and additives.
Barrier Screws
Barrier screws represent a specialized screw configuration designed to enhance the performance of plastic extrusion processes. These screws feature a barrier flight that separates the solid and molten polymer, allowing for more efficient melting and mixing. The barrier flight ensures that only fully melted material progresses through the screw, improving the quality of the extruded product. Barrier screws cater to specific operational needs, offering improved temperature distribution and reduced risk of material degradation. Their design optimizes the extrusion process, making them suitable for applications requiring precise control over material properties.
Impact of Screw Design on Extrusion Efficiency
Performance Metrics
Screw design significantly influences extrusion efficiency. Manufacturers evaluate performance using various metrics. One key metric is throughput rate, which measures the amount of material processed over time. Deep-cut screws with large free volumes often achieve higher throughput rates compared to flat-cut screws with smaller free volumes. This difference highlights the importance of screw geometry in optimizing production speed.
Another crucial metric is energy efficiency. This involves assessing how effectively the screw converts energy into melt temperature and pressure. Efficient screw designs minimize energy consumption while maintaining optimal processing conditions. By analyzing pounds per hour versus RPM, manufacturers can determine the screw’s efficiency in processing materials. This analysis helps in comparing different screw designs and selecting the most suitable one for specific applications.
Innovations in Screw Technology
Innovations in screw technology continue to enhance extrusion processes. Engineers constantly explore new designs to improve performance and efficiency. One notable advancement is the development of longer screws. These screws enhance homogenizing and mixing performance, ensuring a more uniform blend of materials. However, longer screws may also increase the risk of material degradation, necessitating careful design considerations.
Another innovation involves the use of advanced materials and coatings. Manufacturers now utilize high-strength steel alloys and specialized coatings to enhance screw durability and wear resistance. These materials withstand the high pressures and temperatures encountered during extrusion, extending the screw’s service life and maintaining consistent performance.
Industry Insight:
- Advanced Screw Designs in Extrusion explores the impact of innovative screw technologies on extrusion efficiency.
- Material Advancements in Extruder Screws highlights the role of new materials in enhancing screw performance and longevity.
By embracing these innovations, manufacturers can optimize extrusion processes, improve product quality, and reduce operational costs. The continuous evolution of screw technology promises exciting advancements for the extrusion industry, paving the way for more efficient and sustainable manufacturing practices.
The extruder screw stands as a crucial component in the extrusion process, performing essential functions like conveying, melting, and mixing materials. Its design directly impacts product quality and processing efficiency. Advancements in screw technology promise to enhance these aspects further, offering improved performance and sustainability. The industry should continue exploring innovative designs and materials to optimize extrusion processes. By doing so, manufacturers can achieve higher efficiency and better product outcomes, paving the way for future developments in extrusion technology.
See Also
Exploring Various Types of Extruders Available Today
Maximizing Efficiency: Barrel Temperature Tips for Single-Screw Extruders
Jinteng Screw Barrel: Driving Forces Behind Industrial Innovation
Advancements in the Hollow Blow Molding Machine Industry
China’s 75th National Day: Navigating Challenges in Screw Machinery
Post time: Nov-15-2024