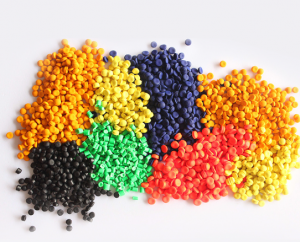
Masterbatch Production and Application Process
1. Production Process
- Raw Material Preparation:
- Resin Base: Select suitable resins (such as PE, PP, PVC, etc.).
- Colorant: Choose high-quality pigments or masterbatch for stable and uniform color.
- Additives: Add antioxidants, UV stabilizers, and other additives as needed to enhance performance.
- Mixing:
- Mix the resin base, colorant, and additives in a specific ratio to ensure even dispersion.
- Melt Extrusion:
- Feed the mixture into an extruder, heating and melting it to form a uniform melt.
- Extrude through a mold to shape it into pellet form.
- Cooling and Pelletizing:
- Cool the melt, solidify it, and cut it into small pellets.
- Packaging and Storage:
- Package the cut masterbatch pellets to maintain quality during transportation and storage.
2. Application Process
- Compounding:
- In the plastic processing stage, mix masterbatch pellets with other raw materials (such as resin and additives) in specific proportions.
- Processing:
- Use injection molding, extrusion, or blow molding to process the mixture into the desired plastic products.
- Final Product Inspection:
- Inspect the final products for color, gloss, and physical properties to ensure they meet standards.
- Market Application:
- Apply the finished products in industries such as packaging, automotive, and home appliances to meet customer needs.
Through these processes, masterbatch effectively imparts the desired color and properties to plastic products, making it widely applicable across various industries.
Post time: Jul-12-2024