Different application fields of various series of blow molding machine products.
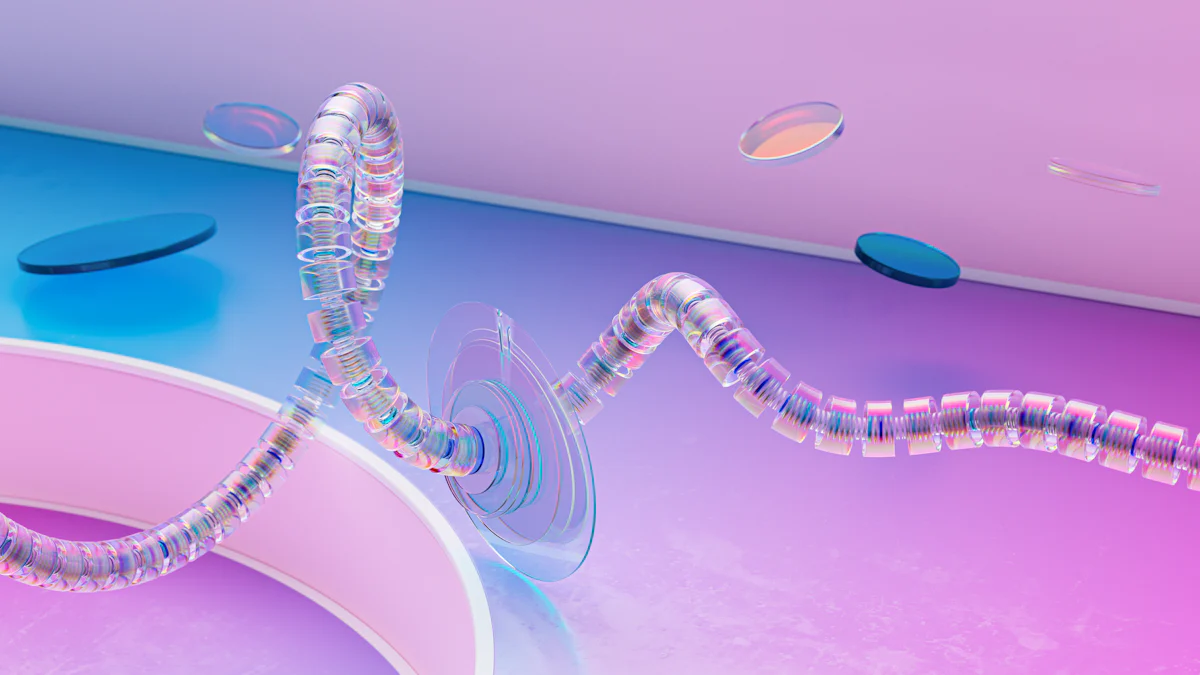
Blow molding machines play a pivotal role in various industries, driving innovation and efficiency. They cater to the growing demand for high-quality, energy-efficient, and customizable plastic products. Industries such as automotive, healthcare, and packaging rely heavily on these machines to meet their production needs. Understanding the application fields of blow molding technologies is crucial for industry professionals seeking to optimize their operations. The versatility of these machines allows for the creation of products ranging from small containers to large automotive components, showcasing their adaptability and importance in modern manufacturing.
Application Fields in the Packaging Industry
Blow molding machines have revolutionized the packaging industry by providing efficient and cost-effective solutions for creating a wide range of containers. These machines cater to the increasing demand for durable and lightweight packaging, making them indispensable in various application fields.
Beverage Containers
Blow molding technology excels in producing beverage containers, offering several advantages over traditional methods.
Advantages of blow molding for bottle production
- Efficiency: Blow molding allows for high-speed production, meeting the demands of large-scale beverage manufacturers.
- Cost-effectiveness: The process reduces material waste, lowering production costs.
- Design Flexibility: Manufacturers can create complex shapes and sizes, catering to diverse market needs.
- Durability: Blow-molded bottles are lightweight yet strong, ensuring product safety during transportation.
Examples of popular products
- Plastic Bottles: Widely used for water, soft drinks, and juices.
- Milk Jugs: Essential for dairy products, offering convenience and freshness.
- Sports Drink Containers: Designed for portability and ease of use.
Food Packaging
In the food industry, blow molding plays a crucial role in ensuring product safety and extending shelf life.
Benefits of using blow molding for food safety
- Hygiene: The process minimizes contamination risks, maintaining food quality.
- Barrier Properties: Blow-molded containers provide excellent protection against moisture and oxygen.
- Customization: Tailored designs meet specific storage and branding requirements.
Case studies of successful applications
- Sauce Bottles: Companies have adopted blow molding to create tamper-evident and easy-to-pour designs.
- Snack Containers: Innovations in blow molding have led to resealable and portion-controlled packaging, enhancing consumer convenience.
Blow molding continues to expand its application fields within the packaging industry, driven by technological advancements and evolving consumer preferences. Its ability to produce versatile and reliable packaging solutions underscores its importance in modern manufacturing.
Application Fields in Medical Devices
Blow molding technology has become indispensable in the medical device industry. It provides precision and hygiene, which are critical for producing safe and effective medical products. The application fields in this sector are diverse, ranging from pharmaceutical containers to custom medical equipment.
Pharmaceutical Containers
Blow molding plays a vital role in manufacturing pharmaceutical containers. These containers must meet stringent standards to ensure the safety and efficacy of medical products.
Importance of precision and hygiene
- Precision: Blow molding allows for the creation of containers with exact dimensions, ensuring compatibility with medical devices and equipment.
- Hygiene: The process minimizes contamination risks, maintaining the sterility of pharmaceutical products. This is crucial for patient safety and product integrity.
- Multi-layer Technology: Recent advancements in blow molding have introduced multi-layer technology, enhancing the barrier properties of containers. This innovation protects sensitive pharmaceuticals from environmental factors.
Examples of medical products
- Syringe Barrels: Essential for accurate dosing and administration of medications.
- IV Bags: Used for fluid delivery, requiring high levels of hygiene and durability.
- Pill Bottles: Designed to protect medications from moisture and light, ensuring their effectiveness.
Custom Medical Equipment
The flexibility of blow molding technology supports the production of custom medical equipment. This adaptability is crucial for meeting the unique needs of healthcare providers and patients.
Flexibility in design and production
- Design Versatility: Blow molding accommodates complex shapes and sizes, allowing for the creation of specialized medical devices.
- Rapid Prototyping: Manufacturers can quickly develop prototypes, facilitating innovation and reducing time-to-market for new products.
- Cost Efficiency: The process reduces material waste, making it a cost-effective solution for custom equipment production.
Innovations in medical technology
- Prosthetic Components: Blow molding enables the production of lightweight and durable prosthetic parts, improving patient mobility and comfort.
- Diagnostic Devices: The technology supports the creation of precise and reliable diagnostic tools, enhancing the accuracy of medical assessments.
- Surgical Instruments: Custom blow-molded instruments offer ergonomic designs, improving surgical outcomes and reducing fatigue for healthcare professionals.
Blow molding continues to expand its application fields within the medical device industry. Its ability to produce precise, hygienic, and customizable products underscores its importance in advancing healthcare technologies.
Application Fields in the Automotive Industry
Blow molding technology has significantly impacted the automotive industry by providing efficient solutions for manufacturing various components. This process ensures the production of lightweight, durable, and cost-effective parts, which are essential for modern vehicles.
Fuel Tanks
Fuel tanks in vehicles require high durability and safety standards. Blow molding technology meets these demands by producing robust and reliable fuel tanks.
Durability and safety considerations
- Material Strength: Blow molding uses materials like high-density polyethylene (HDPE), which offer excellent resistance to impact and environmental stress.
- Leak Prevention: The seamless construction of blow-molded fuel tanks minimizes the risk of leaks, ensuring safety and reliability.
- Regulatory Compliance: Blow-molded fuel tanks meet stringent automotive industry standards, ensuring compliance with safety regulations.
Examples of automotive applications
- Passenger Vehicles: Most cars and trucks use blow-molded fuel tanks due to their lightweight and durable nature.
- Commercial Vehicles: Heavy-duty trucks and buses benefit from the strength and reliability of blow-molded tanks.
- Motorcycles: The compact and efficient design of blow-molded fuel tanks suits the needs of motorcycles, providing both safety and performance.
Air Ducts and Fluid Reservoirs
Blow molding technology excels in producing air ducts and fluid reservoirs, which are crucial for vehicle performance and efficiency.
Efficiency in production
- High Production Rates: Blow molding allows for rapid production, meeting the high demands of the automotive industry.
- Cost-Effectiveness: The process reduces material waste, lowering production costs and enhancing profitability.
- Precision Manufacturing: Blow molding ensures uniform wall thickness and precise dimensions, critical for efficient airflow and fluid management.
Benefits for vehicle performance
- Improved Airflow: Blow-molded air ducts enhance engine performance by optimizing airflow, leading to better fuel efficiency.
- Reliable Fluid Management: Fluid reservoirs produced through blow molding ensure consistent and reliable storage of automotive fluids, such as coolant and brake fluid.
- Weight Reduction: The lightweight nature of blow-molded components contributes to overall vehicle weight reduction, improving fuel economy and reducing emissions.
Blow molding continues to expand its application fields within the automotive industry. Its ability to produce durable, efficient, and cost-effective components underscores its importance in advancing automotive technologies.
Application Fields in Construction and Infrastructure
Blow molding technology has made significant strides in the construction and infrastructure sectors. Its ability to produce lightweight, durable, and cost-effective components has revolutionized how engineers approach various projects. The application fields in this industry are diverse, ranging from water and sewage pipes to insulation and structural components.
Water and Sewage Pipes
Blow molding technology excels in manufacturing water and sewage pipes, offering long-term reliability and cost-effectiveness.
Long-term reliability and cost-effectiveness
- Durability: Blow-molded pipes withstand harsh environmental conditions, ensuring longevity and minimal maintenance.
- Cost Efficiency: The production process reduces material waste, lowering overall costs for infrastructure projects.
- Seamless Construction: Pipes produced through blow molding have fewer joints, reducing the risk of leaks and enhancing reliability.
Examples of infrastructure projects
- Urban Water Systems: Cities utilize blow-molded pipes for efficient water distribution, ensuring a steady supply to residents.
- Sewage Treatment Facilities: These facilities benefit from the durability and leak resistance of blow-molded pipes, maintaining environmental safety.
- Rural Water Supply: Remote areas rely on blow-molded pipes for reliable water access, supporting community development.
Insulation and Structural Components
Blow molding technology also plays a crucial role in creating insulation and structural components, contributing to energy efficiency and sustainability.
Energy efficiency and sustainability
- Thermal Insulation: Blow-molded components provide excellent thermal insulation, reducing energy consumption in buildings.
- Sustainable Materials: The process supports the use of eco-friendly materials, aligning with green building practices.
- Lightweight Design: Components are lightweight yet strong, minimizing the structural load and enhancing building efficiency.
Case studies of construction applications
- Green Buildings: Architects incorporate blow-molded insulation in eco-friendly designs, achieving energy savings and sustainability goals.
- Modular Construction: The flexibility of blow molding supports modular construction, allowing for quick assembly and reduced waste.
- Infrastructure Upgrades: Projects upgrading existing infrastructure use blow-molded components to improve energy efficiency and reduce environmental impact.
Blow molding continues to expand its application fields within construction and infrastructure. Its ability to produce reliable, efficient, and sustainable components underscores its importance in advancing modern construction technologies.
Future Prospects of Blow Molding Applications
The future of blow molding applications looks promising, driven by technological advancements and evolving market demands. As industries seek more efficient and sustainable manufacturing solutions, blow molding stands out as a key player in meeting these needs.
Emerging Technologies
Blow molding continues to evolve with innovations in materials and processes. These advancements open new possibilities for the application fields of blow molding technology.
Innovations in materials and processes
-
Advanced Materials: Engineers are exploring new materials that enhance the strength and flexibility of blow-molded products. High-performance polymers and composites are becoming more prevalent, offering improved durability and environmental resistance.
-
Process Enhancements: Cutting-edge manufacturing techniques, such as 3D blow molding and multi-layer technology, are revolutionizing production. These processes allow for greater precision and customization, meeting the specific needs of various industries.
-
Smart Manufacturing: The integration of IoT and AI in blow molding machines enhances efficiency and quality control. Real-time monitoring and data analytics optimize production, reducing waste and improving product consistency.
Potential new markets
-
Consumer Electronics: The demand for lightweight and durable casings in electronics presents a new opportunity for blow molding. This technology can produce intricate designs that meet the aesthetic and functional requirements of modern devices.
-
Renewable Energy: As the renewable energy sector grows, blow molding can contribute to the production of components for solar panels and wind turbines. The lightweight and robust nature of blow-molded parts make them ideal for these applications.
-
Aerospace: The aerospace industry seeks materials that offer strength without added weight. Blow molding can provide solutions for non-structural components, enhancing fuel efficiency and performance.
Environmental Considerations
Sustainability is a critical focus for the future of blow molding applications. The industry is making strides in adopting eco-friendly practices and materials.
Advances in sustainable practices
-
Recycled Materials: Manufacturers are increasingly using recycled plastics in blow molding, reducing the environmental impact. This practice supports the circular economy by minimizing waste and conserving resources.
-
Energy Efficiency: New blow molding machines are designed to consume less energy, lowering the carbon footprint of production. Energy-efficient technologies contribute to cost savings and environmental sustainability.
-
Biodegradable Polymers: The development of biodegradable materials offers a sustainable alternative for single-use products. These materials break down naturally, reducing pollution and landfill waste.
Impact on industry growth
-
Regulatory Compliance: As governments impose stricter environmental regulations, companies adopting sustainable blow molding practices gain a competitive edge. Compliance with these standards ensures continued market access and growth.
-
Consumer Demand: Increasing consumer awareness of environmental issues drives demand for sustainable products. Blow molding companies that prioritize eco-friendly solutions can capture a larger market share.
-
Innovation Opportunities: The push for sustainability fosters innovation in blow molding technology. Companies investing in research and development can lead the industry in creating new, environmentally friendly products.
Blow molding’s adaptability and commitment to sustainability position it for significant growth in the coming years. By embracing emerging technologies and sustainable practices, the industry can expand its application fields and meet the challenges of a changing world.
Blow molding machines demonstrate remarkable versatility across various application fields, from packaging to automotive and medical devices. Their ability to produce complex, lightweight, and durable products makes them indispensable in modern manufacturing. As industries evolve, the potential for growth and innovation in blow molding technologies remains strong. Advancements in materials and processes, coupled with a focus on sustainability, position blow molding as a key player in future industrial developments. Industry professionals should explore and adopt these technologies to stay competitive and meet the demands of an ever-changing market.
See Also
Advancements In The Hollow Blow Molding Machine Sector
Industries That Depend On Twin Screw Extruders
Various Categories Of Extruders Explained
Overseas Branches Involved In Masterbatch Production
Trends In China’s Machinery: Eco-Friendly Pelletizing Innovations
Post time: Dec-19-2024